For each film
the right high-performance bladeNo two films are the same. Some are tough and elastic at the same time. Additives were used in others. And third parties must be able to withstand impact loads and lateral forces.
In other words, film production is an absolutely high-performance process. And that means that high-performance blades are also required. LUTZ BLADES has been supplying leading film manufacturers with excellent blades for years. We offer replacement blades for the following machine manufacturers, among others: Starlinger®, Kampf®, Windmöller + Hölscher®.
Whether as a razor blade, a 3-hole blade, a carbide blade, a ceramic blade or an exact special shape according to customer drawings: We process different types of steel, carbides and ceramics and adjust our blades precisely to the specific cutting task of the user in terms of material, heat treatment and cutting geometry.
FOR EVERY PLASTIC
the right pelletizing bladeIn the plastics processing industry, granulates are used for the manufacture of plastic parts, in film production, as fillers in concrete and as carrier materials in the pharmaceutical and cosmetics industries. However, the recycling industry is now also one of the producers of plastic pellets and thus provides a valuable service in the circular economy.
Our pelletizing blades, also known as pelletizing blades, are used at the end of the manufacturing process to cut plastics into pellets. LUTZ BLADES has many years of experience in the manufacture of industrial blades for numerous industries and offers a wide range of different blade geometries. Of course, we also develop and produce customized special blades.
Only high-quality materials are used for the pelletizing blades from LUTZ BLADES: They are made of carbon steel or bimetal, with a particularly hard and wear-resistant alloy on the cutting edge.
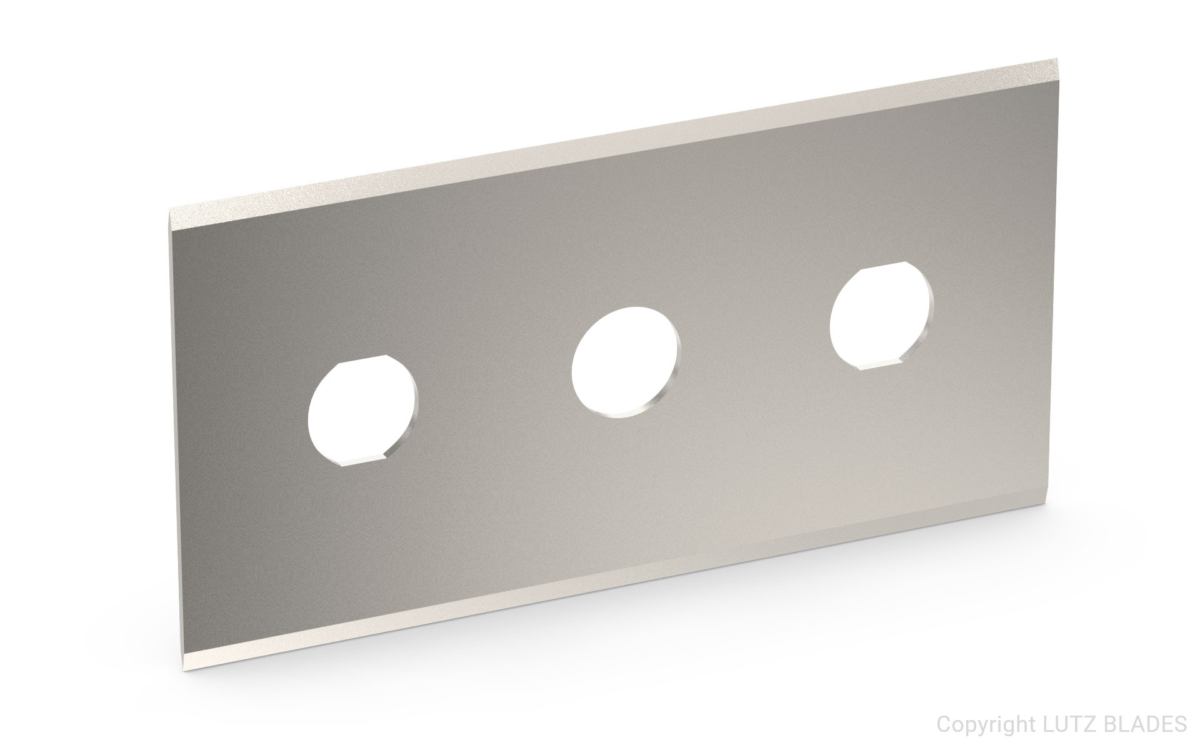
How you benefit
from LUTZ BLADES foil and plastic blades:- Clean cutting edges without edge build-up
- Less cutting dust
- Higher cutting speeds
- Higher productivity thanks to fewer blade changes
This is how
LUTZ BLADES foil and plastic blades from:- Best materials
- Compliance with the tightest tolerances
- Optimum hardness
- Selected high-performance coatings
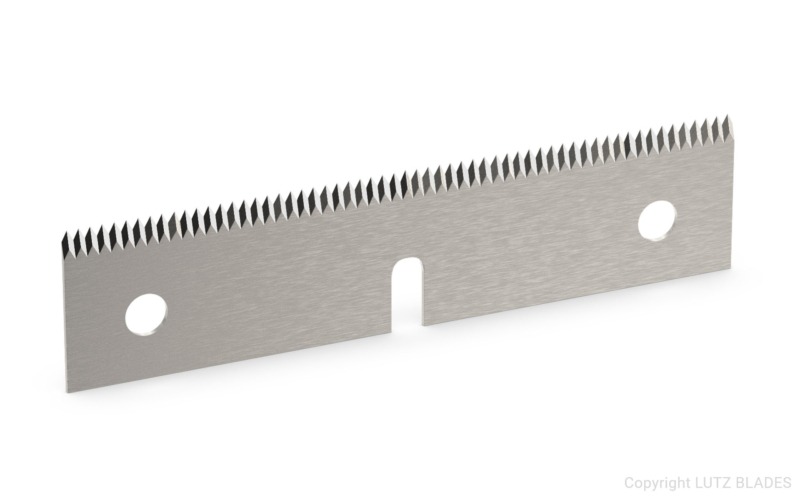
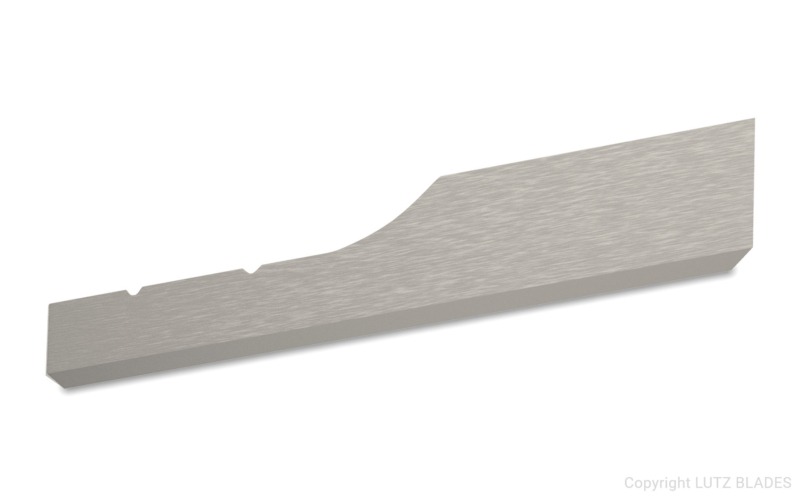
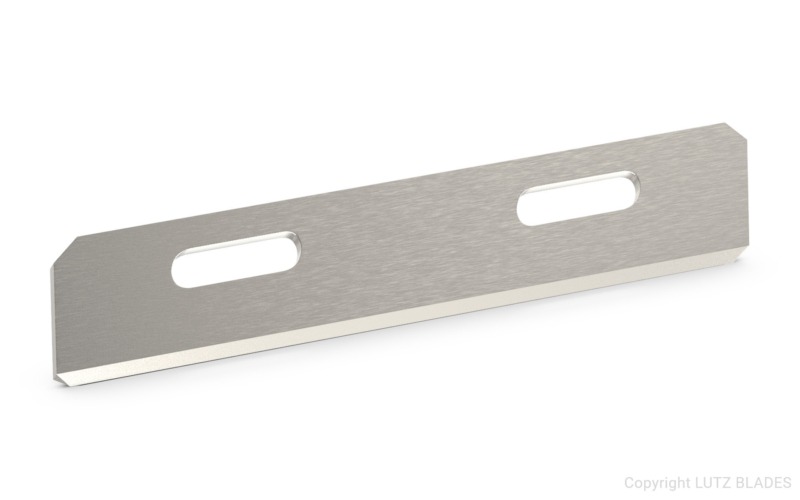


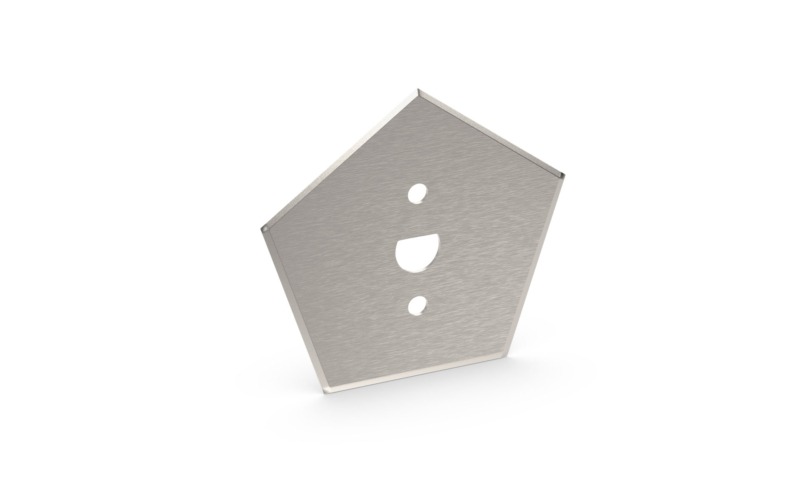
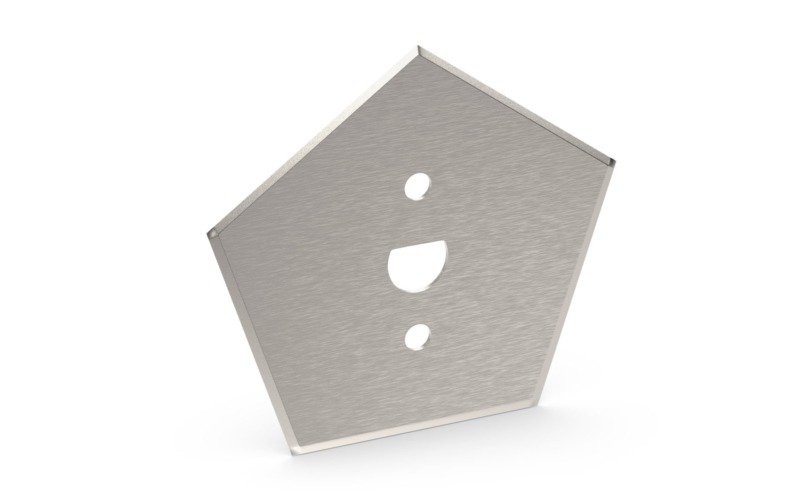

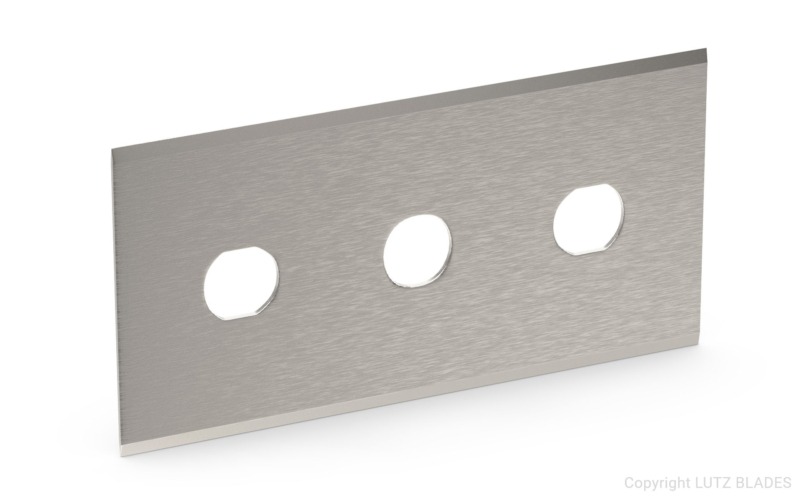
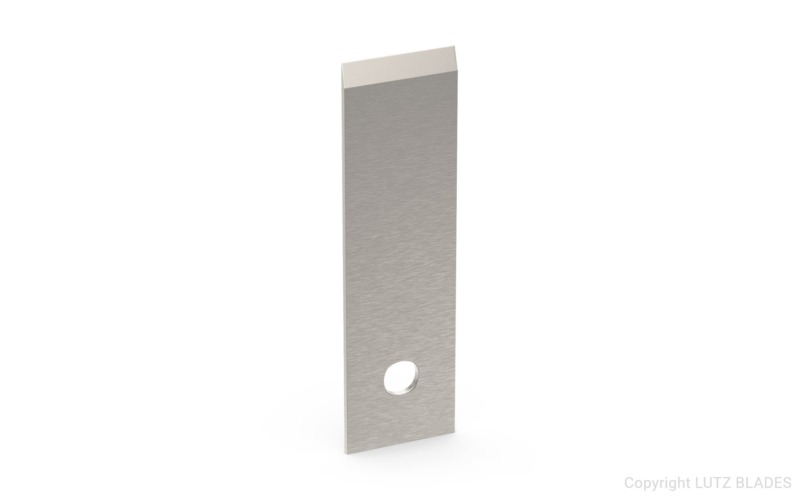
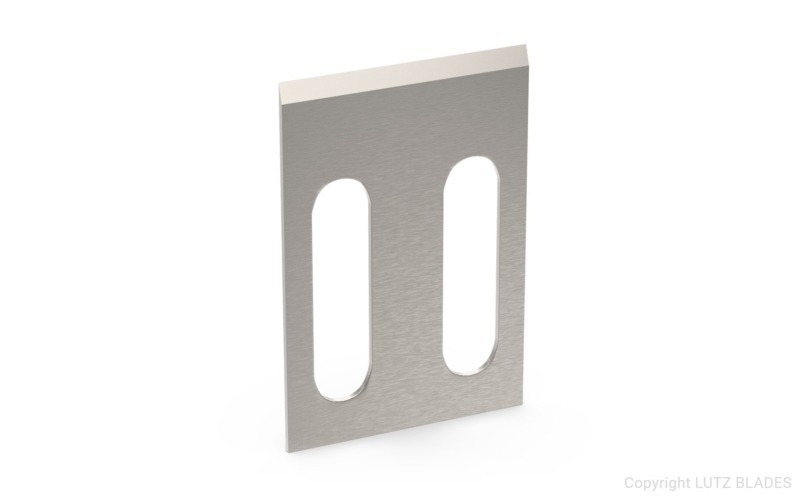
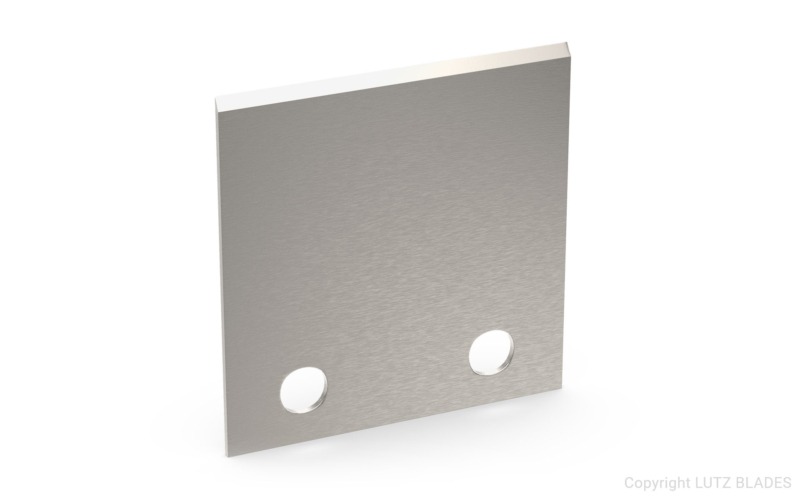
we will help you directly.
Also feel free to use our inquiry form for a quick response.Our experts will be happy to advise you so that you can quickly find your optimum combination of geometry, material, coating and hardness. We have prepared this form so that you can be forwarded directly to the right contact person. Four quick steps are all it takes - and you are in the best hands.
The wide range of materials
for our bladesOur product portfolio offers you blades in thicknesses between 0.06 - 3.0 mm and with final hardnesses between 40 - 85 HRc. You also have a wide choice in our material program:
- Carbon steel
- Rust-resistant, hardened steel
- (HSS) High-performance High-speed Steel
- Ceramic
- Austenite
- Bimetal
- Carbide
The versatile coating program
for our blades
TiN (Titan-Nitrid)
Standard hard material with high wear resistance and relatively high coefficient of friction (against reference material steel approx. 0.4 to 0.7), usually gold-colored, safe application range up to approx. 300 °C.
TiC (Titan-Carbit)
Has lower wear resistance than TiN with significantly lower coefficient of friction (against reference material steel approx. 0.3 to 0.5), usually anthracite colored.
TiCN (Titan-Carbonit)
Intermediate coating material between the high wear resistance of TiN and the low coefficient of friction of TiC, relative position between TiN and TiC depending on the ratio of C and N, usually anthracite color.
TiAlN (Titan-Aluminium-Nitrid)
Has greater oxidation resistance than TiN with comparable coefficient of friction, usually anthracite blue.
ZrN (Zirkon-Nitrid)
With a wear resistance similar to TiN, but denser structure (morphology) than TiN and thus greater resistance to pitting under appropriate load, usually steel colored.
DLC (Diamond-like Carbon)
Has high wear resistance with low coefficient of friction (approx. 0.1 against reference material steel); susceptible to impact loads and high temperatures (between 100 and 300 °C depending on structure).
(PTFE) (Poly-Tetra-Fluor-Ethylen) – Teflon®
Teflon® non-stick coating (PTFE); due to the very low surface tension, practically no foreign bodies stick to the cutting edge, resistant to acids and alkalis; significantly reduced frictional resistance; the very low static friction allows jerk-free cutting (therefore very suitable for the medical sector); low wear resistance; not suitable for contact with sodium and at temperatures above 250 °C.
Color varnish
Applied over the entire surface, serves as a sorting aid for different material thicknesses and as corrosion protection.
Blueing / Blackening
Applied over the entire surface, light corrosion and starch protection, also serves as a distinguishing aid.
Customized quality
The LUTZ BLADES Rapid Prototyping
Do you need a blade that is tailored to your individual cutting process? Which, even if produced in small quantities, has a near-series quality? Our development department has the right answer to these questions: prototype production by LUTZ BLADES.
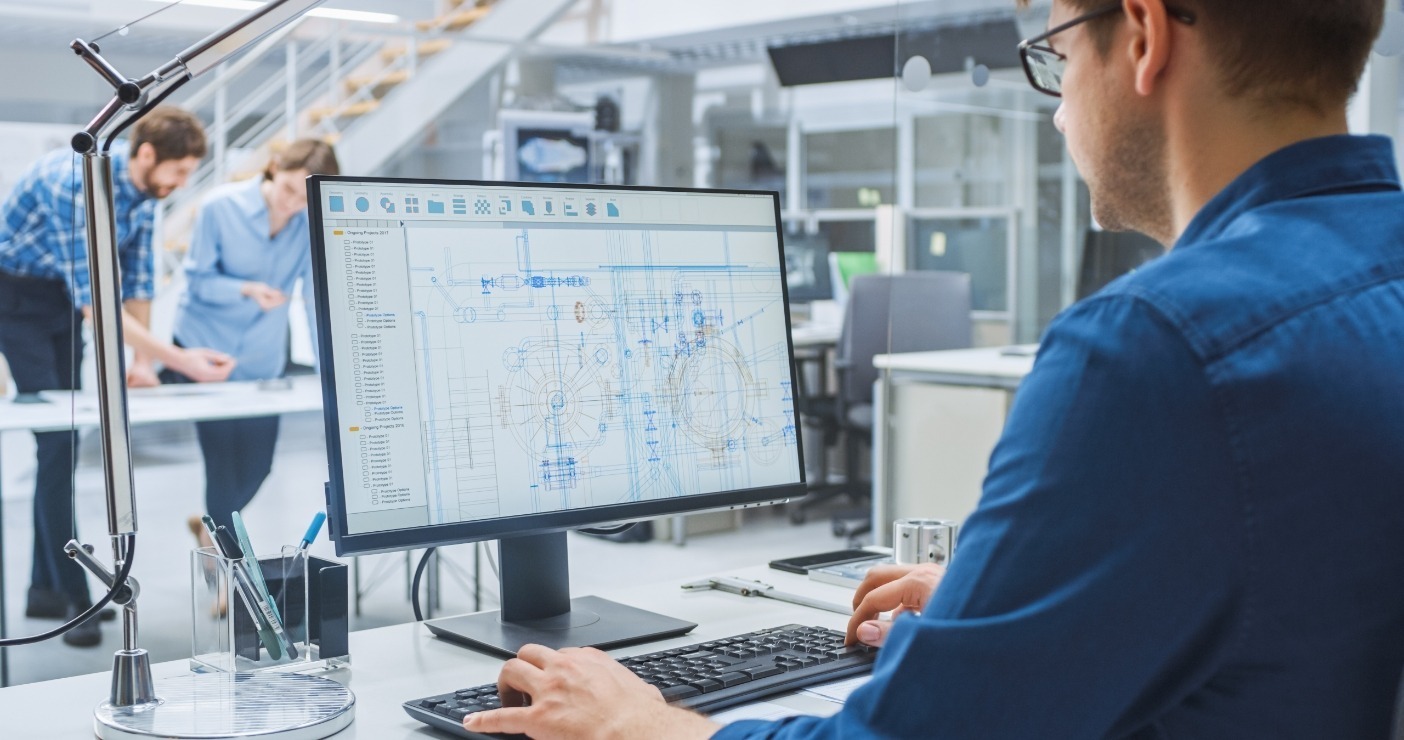
How you benefit
by LUTZ BLADES Rapid Prototyping:- Near-series initial samples
- Maximum flexibility = customized blades
- Smallest quantities possible
- Efficient and accelerated product development
- Development and optimization of the blade before series production

The Lutz BLADES Rapid Prototyping
is characterized by:- Cutting of the blade geometry by state-of-the-art machinery and CNC-based grinding of all radii
- Automatic measurement and testing of the tightest tolerances in the process
- Customized heat treatment and coating
Do you have any further questions?
We are pleased if we can be of further assistance to you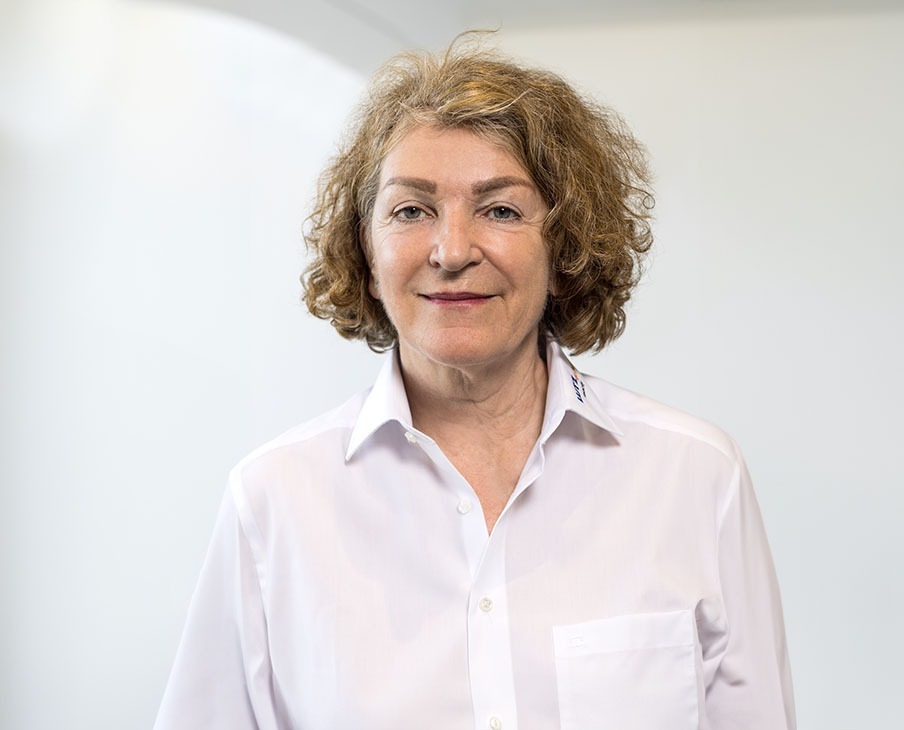